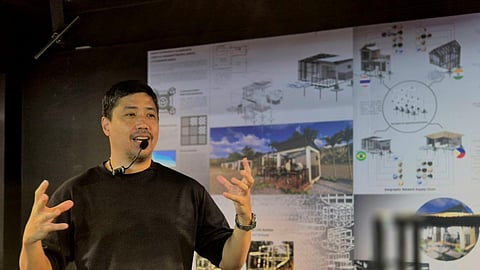
Backed by an investment of $1 million, or roughly P58 million, Singapore-based firm Homeqube is bringing its advantaged homebuilding technologies to the Philippine market to help address the massive housing backlogs nationwide.
At a recent media event, Homeqube founder and CEO Jose Paolo “JP” Calma said the company will officially launch its local operations next month with an ambitious target of constructing a thousand houses in its first year.
Eventually, he said Homeqube will aim to gain at least one percent of the housing market share.
Homeqube’, through its products and services using blockchain and artificial intelligence technologies, will help accelerate local housing construction — a move that will help ease the 6.5 million backlogs in residential spaces.
“Sustainable development has become a common talk among government and business leaders worldwide, and we are bringing that concept to the Philippine property sector with our homebuilding committed to regenerative living,” Calma said.
Calma explained that reliance on traditional building materials, such as steel and cement, contributes to higher property costs as urban migration drives demand.
These materials, which are heavy and complex to transport, can result in extended project timelines of up to 18 months and increased costs due to logistics and middleman fees.
‘Home delivered’
To counter these challenges, Homeqube has launched its Home Delivery Service online, offering Filipinos a streamlined approach to building on any acquired land — beach lots, farm fields, or residential subdivisions.
The service, available on the company’s website, encompasses all phases of the process, from permitting to material acquisition. It is typically completed within two to five months and followed by a swift 30-day installation and delivery.
Homeqube is particularly optimistic about its use of Glass Fiber Reinforced Polymer (GFRP), a material it believes can revolutionize the industry.
GFRP reduces carbon emissions, lowers the environmental footprint of construction projects, and suits Assembly-to-order manufacturing strategies.
The material is also lightweight yet resilient, withstanding winds of up to 310 kilometers per hour and resisting rust. Thus, it can be transported to remote islands.
To support island constructions, Homeqube has invested in a Carbon Kevlar Cargo boat designed for stable, high-capacity transport.
Calma noted that the company’s home kits offer an alternative to traditional steel and cement, allowing for durable homes starting at P1 million.
By selecting regenerative materials, Calma said the company can create a more resilient and adaptable environment, allowing built spaces to evolve alongside clients’ needs.
“In short, we can build regenerative homes anywhere, and our homes can follow where we go,” Calma said.