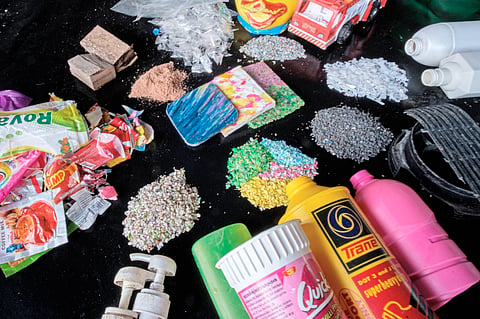
Tackling the plastic waste crisis entails technology. Evergreen Labs Philippines (ELP), a pioneering sustainable waste management solutions organization, employs a range of innovative upcycling technologies to recycle low-value plastics (LVP) like sachets and plastic bags.
In partnership with ReForm Plastic, a social enterprise, ELP transforms LVP into versatile, durable, value-added products for various sectors, including construction and furniture.
ReForm Plastic has developed cost-effective processes that can be applied to various contexts, volumes, feedstock streams and operators. With 14 social franchise factories already in operation or installed across South Asia and Africa, they are empowering local entrepreneurs or organizations while removing unusable waste from the environment.
“We operate across the entire value chain and build collection schemes through our network, including collectors for feedstock securitization. ReForm Plastic together with Evergreen Labs Philippines are continuing to extend our solution portfolio to process and divert all waste streams for a cleaner, more sustainable future,” says Dr. Kasia Weina, ELP director and co-founder.
Upcycling diversion
For ELP’s general waste management work, equipment and infrastructure used are shredders, balers, circular sorting lines, pre-processing equipment (de-labeling, tube-cutter, etc) and low-cost wastewater treatment systems.
ELP also uses head compression molder. This machine transforms LVP into durable boards and sheets by shredding and cleaning plastic waste, and then heating and compressing it in molds to create the products.
Aside from boards for construction, furniture making, and other industries, ELP produces the Eco-grete, a plastic aggregate that can be added to any concrete product.
In the process, LVP are shredded and cleaned. Mineral binders are added into a plastic extrusion process that mineralize the plastic before crushing the aggregate into the desired size.
The mineralized plastic has stone-like properties and replaces mined gravel in concrete products such as pavers, blocks, tiles, and wall panels with similar properties to traditional products.
Digital tool
ELP builds and implements plastic waste collection programs, as well as activates communities, schools, businesses, and local government units (LGUs) to participate in waste segregation and collection initiatives.
It uses a track and trace tool from ASM Global, a digital solution provider and software developer. The digital tool enables seamless traceability, reporting and audit of ELP’s waste value chains and issuance of collection and diversion certificates in compliance with Extended Producers Responsibility (EPR) regulations in the Philippines.
“This software is applicable from web and via app and is provided free of charge to all partners working with ELP,” said Weina.
“We currently jointly develop the system for global use after successful implementation in the Philippines,” she added.
Additional techs
ELP is further diversifying its output product portfolio and serve different markets so new processes would be adopted, according to Weina.
“Considering that wood plastic composite has gained popularity over the last years, we are in trials to produce planks for decks, jetties and boardwalks from low value plastic through extrusion-compression molding,” says Weina, adding that the first tradable products are expected in the fourth quarter of the year.
“To increase production efficiencies, we are planning to add a continuous board production process from low value plastic. Current processes do not allow for mixed materials to be used or boards to be produced directly from flakes, so we have to develop this in house. We would love to partner with engineering companies or universities fur future developments,” she says.
Lastly, we are carefully analyzing the pyrolysis market, which in principle enables the conversion of plastic back into oil and gas, according to Weina.
“The oil can be refined into diesel, kerosene or petrol but the process is costly and cannot handle all types of plastic. There are many failed projects around the world, including the Philippines so we will wait with any such deployment until a reliable solution is available,” says Weina.